Solar panel assembly is a critical stage in the production process, during which individual solar cells are integrated into integrated modules that can generate electricity efficiently. This article will combine the MONO 630W product to take you on an intuitive tour of OCEANSOLAR's production plant and learn about the production process of solar panels in detail.
MONO 630W Bifacial TransparentBacksheet
Serial connection and wiring
OCEANSOLAR solar panels use high-efficiency cells as raw materials. Only high-quality raw materials can have a longer quality assurance. Before assembly, we will use high-precision machines for screening and slicing.
The assembly process starts with serial connection and wiring:
Serial connection: Use metal ribbons to connect individual solar cells in series. This involves welding metal contacts on each cell to ensure efficient current flow. The cells are carefully aligned to form strings, thereby maximizing the overall electrical output of the panel.
Wiring: This step ensures that the cells within the string are firmly connected. Wiring involves placing additional metal ribbons on the cells to further enhance the electrical connectivity and stability of the string.
Lamination and lamination
OCEANSOLAR will also adjust the corresponding lamination methods when dealing with different products to ensure the quality of the products.
After the cells are strung together, they are laid up and laminated:
Layering: The interconnected cell strings are carefully placed on a layer of encapsulant material, usually ethylene vinyl acetate (EVA). This material helps protect the cells and provides mechanical stability. The cells are arranged in a specific pattern to ensure optimal spacing and alignment.
Lamination: The layered assembly consists of encapsulant material, solar cells, and additional encapsulant layers, sandwiched between a glass sheet on the front and a protective backsheet. The entire stack is then placed into a laminator, where it is heated and vacuumed. This process bonds the layers together, ensuring that the module is durable and weather-resistant.
Frame
Unlike other manufacturers, OCEANSOLAR uses a thickened aluminum frame for support. Although it will increase the cost, we are happy to do so for the sake of better products for our customers.
After lamination, solar panels need a frame for structural support:
Frame: The laminated modules are mounted in an aluminum frame. The frame not only provides rigidity, but also protects the edges of the panel from mechanical damage and environmental factors. The frame usually includes mounting holes, making it easier to install the panel on a roof or other structure.
Sealing: Apply sealant between the laminated module and the frame to prevent moisture intrusion and extend the life of the panel.
Junction box installation
In order to make OCEANSOLAR's customers have a better and more convenient installation, OCEANSOLAR provides customers with a variety of connector lengths to cope with all installation situations that customers may encounter.
The junction box is a key component to facilitate the electrical connection of the solar panel:
Junction box: The junction box is installed on the back of the solar panel. It is equipped with electrical connectors and diodes to prevent current backflow, which can damage the cells. The junction box is firmly sealed to prevent moisture and dust.
Wiring: The cables of the junction box pass through the frame, providing a method to connect the panel to the entire solar system.
Quality testing
The assembled solar panels undergo a series of quality tests before shipment to ensure their reliability and performance: OCEANSOLAR has more than two EL tests, more than two appearance tests, and final power tests during the production process, which really achieves layer-by-layer control.
Appearance inspection: A thorough visual inspection is carried out to check whether the panel has defects such as cracks or misalignment.
Power testing: Testing the panels under simulated sunlight conditions to measure their electrical output and efficiency. This includes flash testing to verify that the panels meet their rated power output.
EL test inspection: Detect internal defects, cracks, debris, cold solder joints, broken grids, and abnormalities of monolithic cells with different conversion efficiencies in solar cell modules by simulating the entry of current.
Conclusion
The assembly of OCEANSOLAR solar panels is a meticulous process that combines precision engineering and advanced manufacturing techniques. By carefully connecting and protecting solar cells, manufacturers produce durable and efficient solar modules that can generate clean energy for decades. This assembly process ensures that solar panels are not only high-performance, but also reliable and durable, contributing to the global shift to renewable energy.
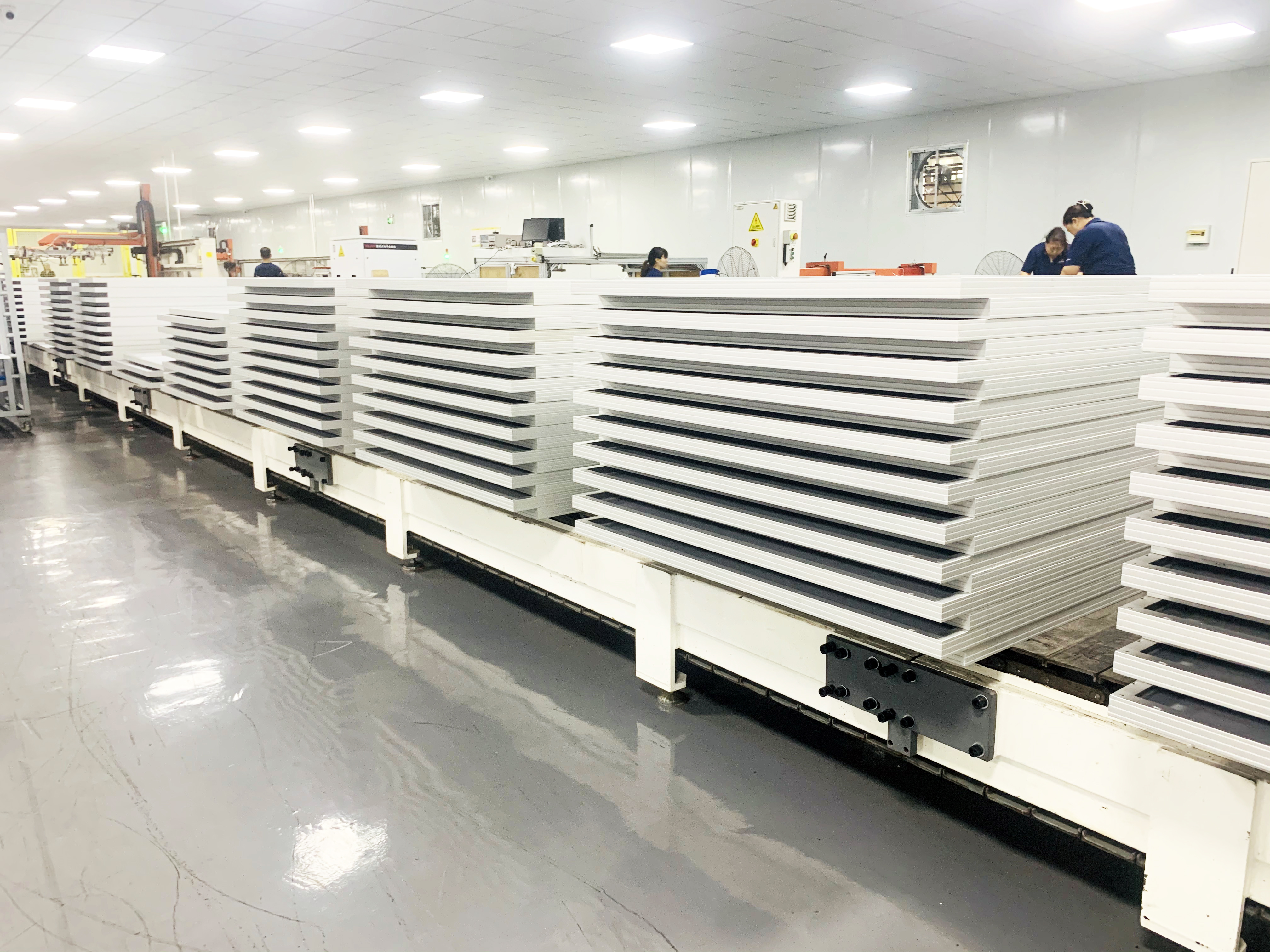
Post time: Jul-18-2024